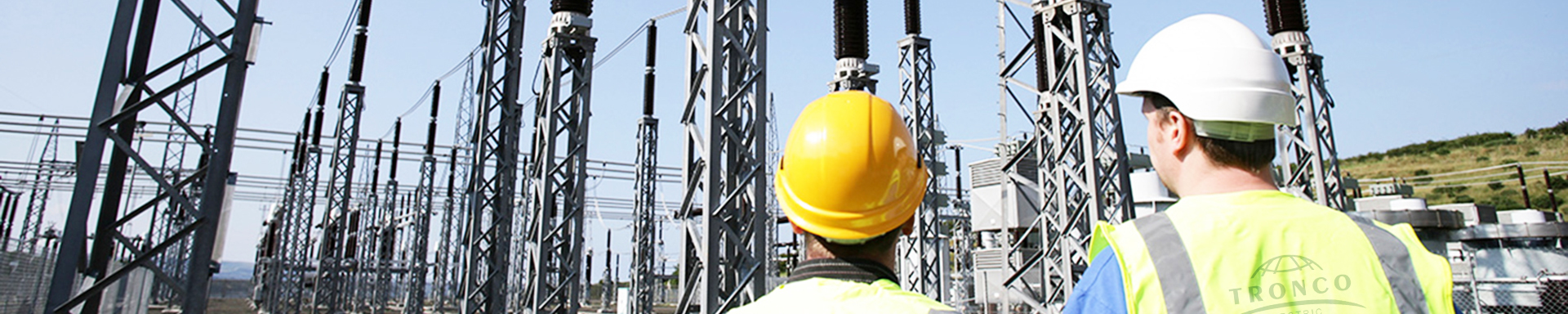
RTV Silicone Coating Insulators
2023-03-06 22:30RTV silicone anti-pollution flashover coatings have been used extensively for years – initially mainly on post insulators and bushings at substations and more recently also for porcelain or glass string insulators on transmission lines. One of the reasons why the latter use has been relatively limited in the past has been working height and field conditions that make it a challenge to ensure consistent quality and evenness of spraying.
In the Q1, 2015 issue, Alberto Pigini's Column discussed the topic of glass disc insulators coated with RTV silicone rubber in the factory. He estimated that more than a million such factory-coated discs were already in service worldwide but noted that this data did not include China. This column will therefore help complete the picture by reviewing progress in China when it comes to factory pre-coating RTV silicone material onto insulators.
There have already been years of positive application experience in this country as far as coating glass or porcelain transmission line insulators with RTV silicone. Methods adopted for coating, mainly at working height on transmission lines, have included spraying and brushing. While both have proven difficult due to working height that made it hard to ensure consistent quality, significant improvements in pollution flashover performance of glass or porcelain insulators were nevertheless achieved.
Presently, a number of UHV DC and AC transmission lines are under construction in China and, apart from composite insulators, these lines are also being equipped with glass and porcelain string insulators. In this regard, the State Grid Corporation of China now requires suppliers of glass and porcelain UHV insulators to provide units with factory pre-coated RTV silicone at time of shipment. Glass and porcelain insulator manufacturers who already have frame orders with the SGCC are therefore co-operating closely with manufacturers of RTV coatings to fulfill this requirement.
In terms of anti-pollution flashover performance and contribution to system reliability, factory dip coating of glass or porcelain discs rivals composite insulators.
Initially, some manufacturers adopted a spray-on process while others used dip coating. In fact, several suppliers of RTV coating material have developed their own dip coating equipment and processes, each with their own features and benefits. Common points are achieving large production scale and high coating quality. Compared with spraying, dip coating is more environmentally sound since it does not cause the same level of air pollution while reducing wastage. In many cases, the end quality of insulator coating is better than achieved by spraying. For these reasons, dip coating now dominates the Chinese market, where it is believed that some one million factory pre-coated glass or porcelain UHV insulator discs are already in service. Moreover, based on equipment used for dip coating string insulators, several RTV material manufacturers have now developed similar equipment and processes for station post insulators.
In terms of anti-pollution flashover performance and contribution to system reliability, factory dip coating glass and porcelain disc insulators can rival composite insulators. Each solution offers it own features, however the lower cost of composite insulators is still a significant advantage. As such, there is a need to reduce the costs of factory dip coating RTV material to make this technical solution as competitive as possible.
www.inmr.com-coating-insulators-with-rtv-silicone