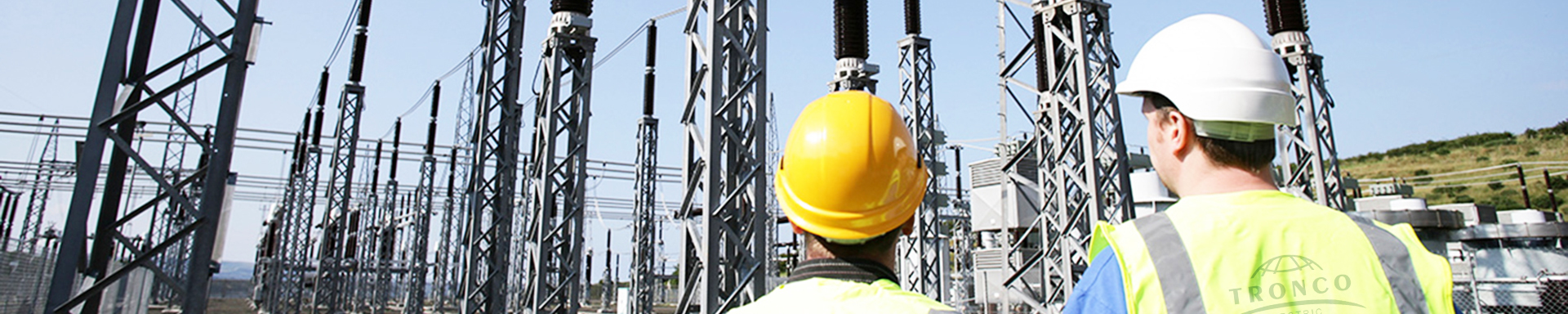
- Home
- >
- News
- >
- RTV Coating insulators
- >
RTV Coating insulators
2024-12-19 14:54Anti-pollution flashover RTV coating insulators are mainly used for external insulation of power substations and transmission lines, power plants and substation equipment, and other electrical equipment to prevent pollution flashover. After using this RTV coating on the insulator, a composite porcelain insulator or glass insulator with anti-pollution flashover coating is formed, which is to improve the external insulation configuration of power transmission and transformation equipment. It is suitable for external insulation anti-pollution of substations and overhead transmission line equipment operating under dirty conditions at ambient temperatures of -50°C~100°C, various voltage levels of AC and DC systems, to prevent flashover and improve the external insulation level of equipment.
Manufacturing requirements:
Completely solve the environmental pollution caused by manual spraying and the out-of-control of spraying quality. The finished product has super self-cleaning, hydrophobicity and hydrophobic migration, adhesion, and steep wave impact resistance, meeting the needs of safe operation of power transmission and transformation.
Manufacturing materials: Anti-pollution flashover coating series products
Manufacturing environment: Dust-free, windless, ultra-constant temperature, constant humidity 20,000 square meters high-standard manufacturing workshop
Manufacturing capacity: 20,000 disc insulators and 300pcs porcelain post insulators and hollow insulators per day
Manufacturing environment control system: multi-station automated dip coating, Lilin-style curtain coating; self-cleaning, highly hydrophobic anti-pollution flashover coating, automated dip coating robot
There has been growing worldwide interest in applying RTV silicone coatings to mitigate pollution-related flashovers of ceramic insulators that suffer poor pollution performance due to inappropriate selection or insufficient self-cleaning. Such a solution is usually based on various criteria, including effectiveness in suppressing leakage current, maintaining hydrophobicity and satisfactory adhesion, and minimizing arc degradation or surface damage due to discharges. Studies have demonstrated that there can be significant differences between different RTV coatings available on the market in terms of their long-term performance, especially after aging in a harsh desert environment.
Given this, special effort was devoted to selecting the most suitable coating type and formulation, including the most reliable primer as the bonding agent. Our implementation team then looked to this solution to minimize pollution-related leakage current while optimizing the costly and time-consuming remedial measures used in the past. Testing confirmed that the RTV formulation showed exceptional adhesion properties and was virtually impossible to remove from coated surfaces after curing.