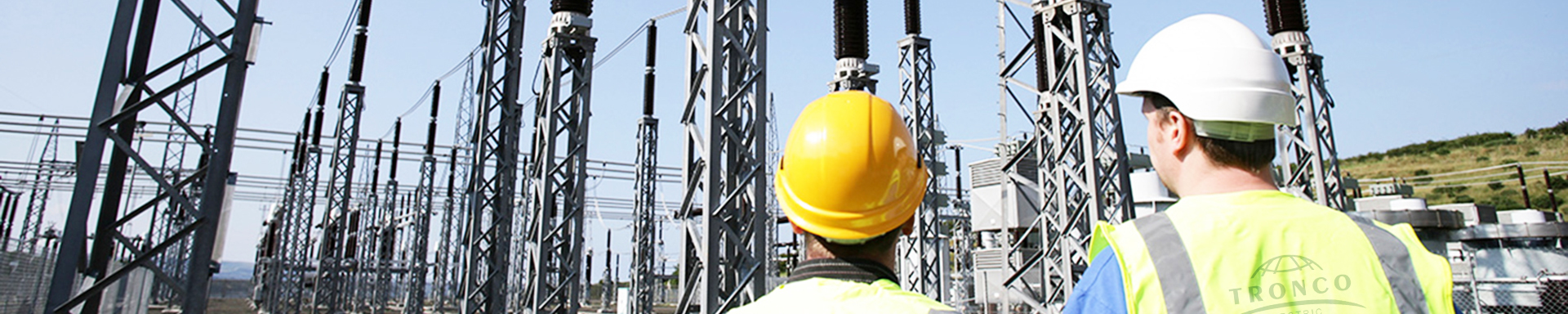
Solution for the interface sealing of composite insulators
2023-05-10 15:24In the connection area at the end of the composite insulator, use high-temperature vulcanized silicone rubber to mold the metal fittings and mandrel together directly. This new technology has a simple structure, easy production, safe and reliable use, avoids the quality defects in the above analysis, and improves the anti-aging performance. Because it is molded with high-temperature vulcanized silicone rubber, the sealing process is reduced, the interface is reduced, the sealant is saved, the sealing performance is improved, and the brittle fracture of the mandrel that is easily caused by moisture due to poor sealing is solved. question. Even more gratifying is that after adopting this structure, under the same conditions, the dry arc distance and creepage distance are effectively increased, and the lightning impulse withstand voltage level is improved. According to the laboratory test results, it can be increased by more than 15%. In thunderstorm-active areas and vast mountainous areas, under the condition that the height of the structure remains unchanged, the use of this structure can increase the lightning flashover voltage and ensure the safe operation of the power grid.
Traditional composite insulators are sealed by manual sealing. The rubber used is room-temperature vulcanized, which has low anti-aging performance. Especially in harsh environments, electric corrosion will make the sealant age faster, and the sealing process is not easy to control. The mandrel is corroded and accidents occur; and the new sealing process can improve the safety factor of the composite insulator in the operation of the power grid, prevent accidents caused by poor sealing, and will be more reliable in product quality!