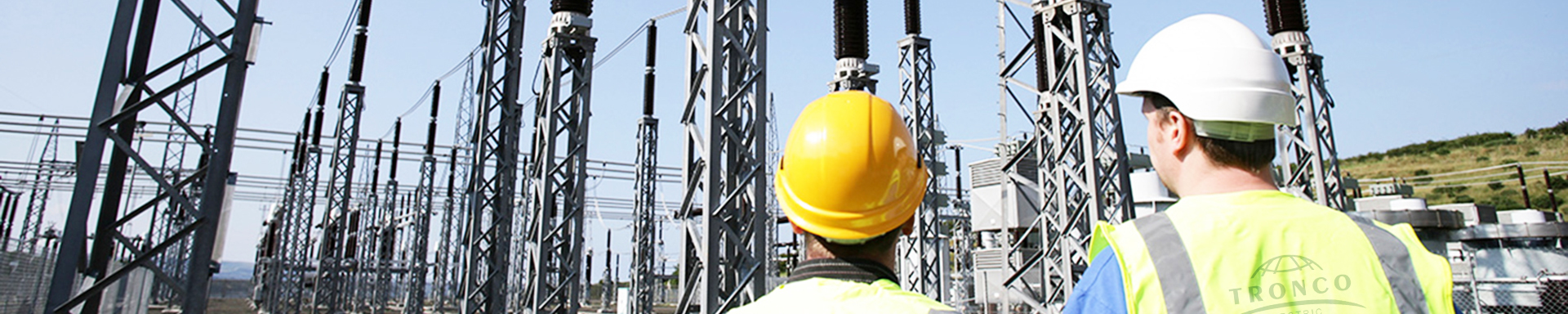
RTV Coatings on Ceramic Insulators
2022-11-07 20:54Different types of insulators with hydrophobic properties have now become commercially available, including composite insulators, hybrid insulators, and silicone-greased ceramic insulators. One variant of rapidly growing interest and application worldwide involves coated insulators obtained by applying a uniform thin layer of Room Temperature Vulcanizing silicone rubber material along a ceramic insulator's surface. Coated ceramic insulators offer the advantage of a surface with the desirable characteristics of a hydrophobicity transfer material to provide improved withstand voltage capability under pollution coupled with the known mechanical robustness and strength of the underlying ceramic.
RTV silicone is a liquid polymer that vulcanizes when exposed to moisture in the air. By all accounts, there can be considerable variation in the electrical and physical properties of different commercially available coatings. Such variations depend on factors including but not limited to the relative amounts of reinforcing fillers in the coating, curing components that affect the degree of cross-linkage in the polymer, and primers for improving adhesion to the insulator surface. Optimal coating thickness can be yet another variable among different suppliers.
Silicone polymers and molded components made with silicone elastomers exhibit low surface energy that does not allow water to spread out over the surface. These elastomeric formulations contain a small but not negligible amount of low molecular weight siloxane chains that continually migrate to the surface – a phenomenon that not only promotes sustained hydrophobicity even in presence of pollution but also encapsulates the pollution layer. RTV coatings can be used on both station insulators and line insulators and can be applied to an insulator either wholly or partially using spraying or dipping.
Most early applications of RTV silicone coatings were conducted on-site as a remedial measure to mitigate pollution flashovers on insulators and bushings that demonstrated poor service performance. On-site coating, whether manual or robotized, is still the most commonly used practice for station insulators. However, in the case of line insulators coating application in situ can be challenging due to challenging working conditions and because of the difficulty in applying the coating evenly. As a result, there has been growing interest to adopt factory pre-coated cap & pin string insulators as one of the possible solutions adopted during the design phase of a new line project.