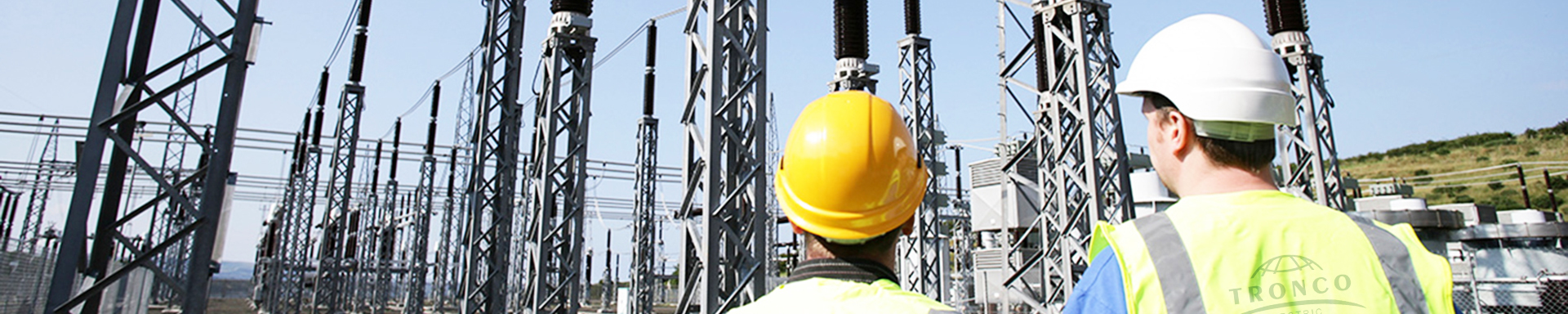
- Home
- >
- ORDER EXECUTION
- >
ORDER EXECUTION
As a critical element of order fulfillment, order execution is the workflow that ensures customer orders are properly prepared and delivered to the correct place.
Raw material order placement: When the sales department receives orders from customers, the order details (including types, quantities, consignee details, and necessary information) are sent to the order management system.
Picking Inventory accessories: The process of collecting specified quantities of items from inventory to fulfill customer orders. Order picking must be a highly controlled process as it directly affects the productivity of the entire order processing workflow, the earlier parts are picked accurately, the sooner they can be scheduled for production, packed, and shipped.
Sorting: This is the separation of picked items according to their destination. Each model is sorted into its respective order prior to packaging and shipping. Sorting is an important step in improving accuracy and customer satisfaction, as this is the best time for workers to ensure that all ordered items are present and in good shipping condition.
Packing: The procedure of packing securely and completely into appropriate shipping cases. The packing process also includes weighing and making shipping marks on it. Whether items are packaged custom or plain, it is important to prioritize sizes and weights that are easy to handle and cost-effective.
Shipping: The process of shipping an order to its final destination. Orders can be delivered directly to the port or to the port of destination. If you combine orders, you can save on shipping costs to the greatest extent.
After the item is delivered, the logistics department typically follows up with the customer to ensure satisfaction or to answer any questions about the product purchased. Customers are more likely to be satisfied if the order processing steps are performed efficiently—meaning that all items are delivered accurately, on time, and safely.