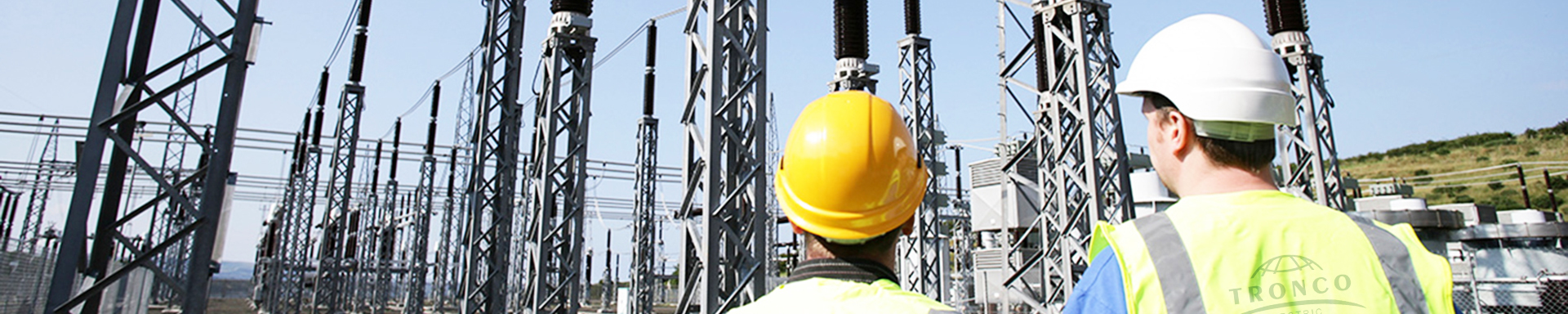
DIFFERENT PERFORMANCE OF AGED INSULATORS AMONG PORCELAIN, GLASS AND COMPOSITE INSULATORS
2023-03-08 10:37Utilities have three proven insulator technologies they can deploy on their networks. Porcelain and toughened glass insulators have been around since the first days of overhead power delivery and have a demonstrated record of high reliability. Composite insulators, by contrast, were introduced on a large scale only about 35 years ago but have since made rapid strides to be considered alongside with porcelain and glass. Still, there are important differences in these insulators. For example, both porcelain and glass are easily wettable, brittle, and heavy materials, whereas composite insulators are light, non-brittle and discourage water filming for extended periods of time. However, since the outdoor conditions and the conductors they support are the same, line design in terms of insulator dimensions and electrical and mechanical strengths is virtually the same for the different insulator technologies. They also have several common national and international standards within ANSI and IEC. While many users feel that the operation of lines with aged insulators and maintenance practices on these lines should also be the same for all insulator technologies, nothing could be further from the truth. All similarities between the different technologies should end once insulators are no longer in their new condition. This is because the various service stresses (electrical, mechanical, environmental, etc.) can produce significant differences in insulator performance over time.
Many users expect these insulators to last over 50 years and this has indeed been demonstrated for toughened glass and some porcelain. Still, they are known to fail occasionally due to problems originating from manufacture, misapplication, contamination, and vandalism. At the same time, failure modes of porcelain, toughened glass, and composite suspension insulators are different, and relevant failure rates vary accordingly. In most cases, differences in failure modes are related to the materials and the manufacturing methods used. More important than the failure rate is the impact of a single failure on system reliability.